APS - advanced Planning & Scheduling
A clear and accurate plan will lead to operational efficiency
Decision making in a dynamic environment
Maximum flexibility within an organized and secured data environment
Previous slide
Next slide
A clear and accurate plan will lead to operational efficiency
Decision making in a dynamic environment
Maximum flexibility within an organized and secured data environment
A clear and accurate plan will lead to operational efficiency
Decision making in a dynamic environment
Maximum flexibility within an organized and secured data environment
Previous slide
Next slide
[ditty_news_ticker id="646"]
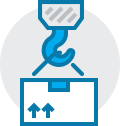
Production Planning & Scheduling
Production planning & Scheduling is the iterative process of achieving optimal response to demand through production efficiency improvements.
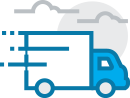
Distribution Planning
Distribution problems are those that require guaranteed delivery time windows when the occasional delivery tasks are not known...

Workforce Scheduling
Almost every organization is engaged in management and human resource scheduling. Transparency and objectivity of workforce scheduling...
- Scheduling software for production planning, distribution planning, workforce schedule and other applications.
- User-friendly, with a variety of information views according to each customer’s needs.
- Has been successfully implemented in many productive factories in Israel and worldwide since 2002.
- Built-in connectivity for different information & ERP systems.
- A decision support system that can be adjusted to meet different planning needs.
- Improving efficiency and reducing production costs through accurate and detailed planning.
- Raising customer satisfaction by improving compliance with delivery times – OTD.
- Reduced planning time and efforts while quickly detecting exceptions and alerts.
- Order and structural improvement within the information system by adjusting scheduling related data.
- Improved Internal communication achieved with transparency and understanding of mutual influences.
- Decision making will become simpler while using the common planning portal.